Get this deal! Call now.
Speak with a vehicle protection plan specialist and get $300 off any new contract instantly.
Call 866-678-4172
or scan the code below
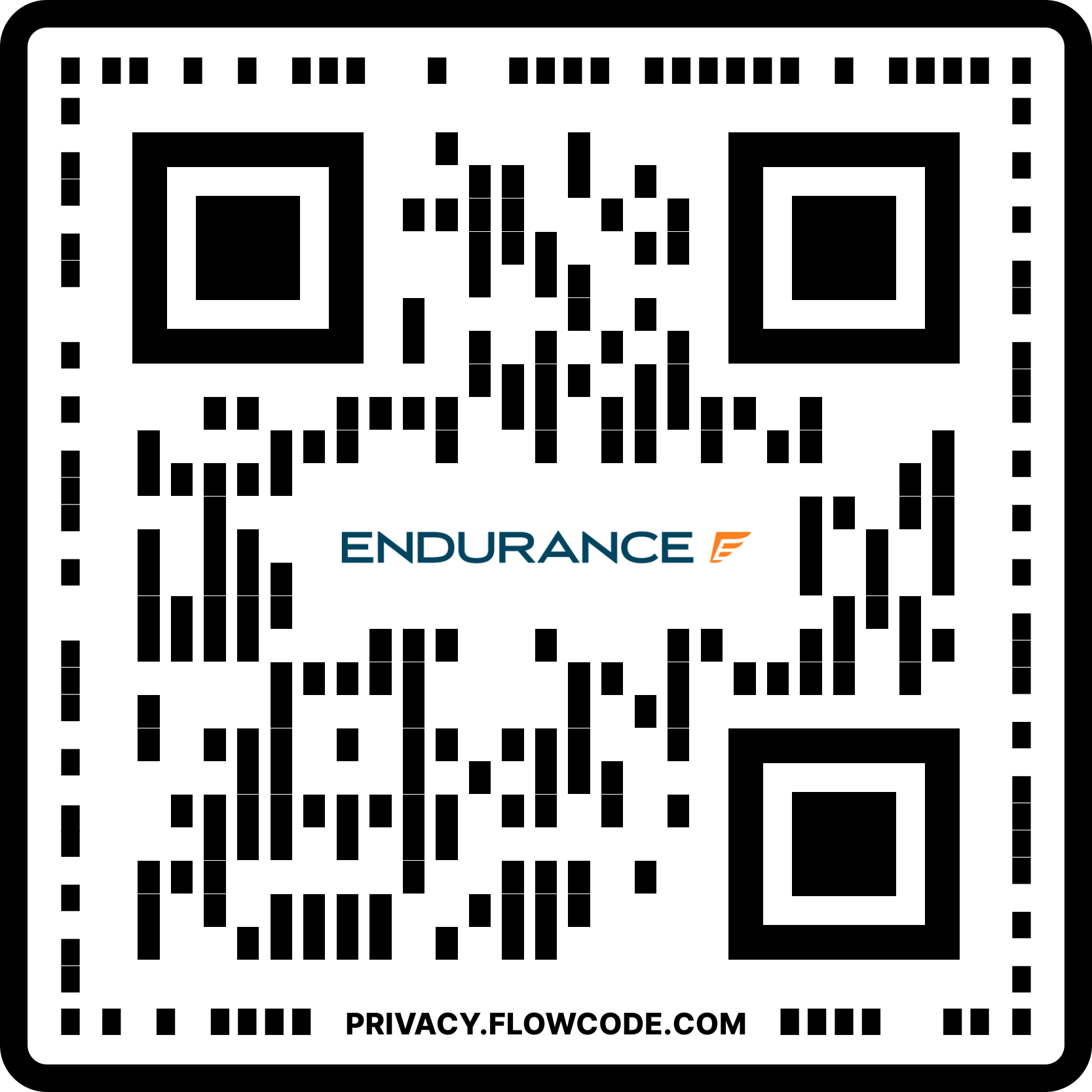
Owning a vehicle comes with many responsibilities, among them dealing with regular maintenance and repair issues. These tasks range from scheduling an oil change to dealing with a dreaded check engine light. The typical driver drops off their ride at the auto repair shop without much thought about what goes on behind the scenes. While there’s nothing wrong with this carefree approach (assuming you have a trusted mechanic), understanding how auto repairs work will save you time, money, and frustration. This modest extra effort doesn’t require going to technician school (that takes years) but involves examining basic repair shop operations.
We’ll walk you through the entire repair process, from drop-off to pick-up and everything in between. You learn the importance of diagnostics and how a service center compiles its sometimes surprising repair estimates. We’ll also cover how costly repairs can be avoided with an extended warranty.
Why should you know these details? Because car repairs are getting more expensive. CNBC reported that automotive repair bills increased by 20% in 2023 over the previous year. In 2024, the U.S. imported almost $88 billion in automotive parts and accessories, which are potentially vulnerable to tariffs, leading to higher costs for car owners. In other words, keeping a vehicle on the road isn’t getting any cheaper.
The first part of the car repair journey involves arriving at the service center. Here, communication is essential, as the technician or service advisor will ask detailed questions about why you brought the car into the shop. Typical inquiries include:
Depending on the shop, the questions will be accompanied by a brief visual inspection, which will look for obvious trouble spots like fluid leaks or damaged components. A check engine light may include an on-the-spot check with an OBD II scanner (or an on-board diagnostics, second generation scanner). This initial assessment helps the shop target specific systems for attention, including assigning a particular auto mechanic who’s experienced with your make and model or has specific skill areas.
Just like visiting a doctor when you’re unwell, a repair shop needs as many facts as possible to diagnose the problem comprehensively. It’s vital not to underestimate the importance of this consultation. Providing crucial clues can speed repairs and minimize diagnostic costs. For example, just saying you hear a noise while driving isn’t overly helpful, but saying this sound occurs while turning at a low speed may point to an issue with the front suspension.
Think of the diagnostic process as detective work, but today’s mechanics are just as likely to use sophisticated detection equipment as visual inspections. Modern automobiles are rolling computers, with dozens of electronic systems, including sensors and control modules. Add millions of lines of computer code, and it’s clear this isn’t your grandfather’s automobile. Even somewhat simple repair issues require advanced diagnostic tools to get to the root of the problem. Many vehicle systems, including HVAC, brakes, steering, engine, transmission, and emission controls, depend on computers for smooth operation.
An OBD II scanner is the most commonly used diagnostic tool. This device connects to a vehicle’s diagnostic port and retrieves any diagnostic trouble codes (DTCs) that are stored in the car’s computer system. Any vehicle built since 1996 has an OBD II port. The presence of a DTC is often what triggers a check engine light. Unlike the inexpensive code readers you can purchase (which is a good tool to have anyway), a mechanic’s OBD II scanner provides a higher level of detail about the car’s operating status. Not only does it detect DTCs, but it can also provide live data about engine operation, transmission function, electrical system condition, emissions control, sensor function, and control module status.
Yet, an advanced OBD II scanner isn’t a magic bullet for diagnosing car trouble; it’s a starting point. Often, a code scan points a technician in a general direction, but more work is involved. For instance, DTC P0301 indicates a misfire in engine cylinder #1. The problem could be a worn spark plug, a defective fuel injector, internal engine damage, or one of several other causes. A mechanic has to rule out all of these potential problem areas.
Many technicians will also rely on extensive repair databases (such as ALLDATA or Identifix) that catalog make- and model-specific repairs. These resources help identify the most likely causes while outlining repair procedures.
After the diagnosis is complete, the shop will prepare an estimate for the service work. Depending on the business, you may receive this information by phone call, text, or email. The estimate is based on a formula that includes:
The labor hours are based on industry-standard guidelines that can vary by vehicle. A repair in one car can cost more than the same work in a different automobile. Let’s take the case of replacing the alternator, a common repair in older vehicles. RepairPal estimates that the labor alone for this work in a 2010 Honda CR-V is $177 to $266, while running $110 to $161 for a 2010 Toyota RAV4.
Why the difference? Because the CR-V’s alternator is buried below the engine and sandwiched between the power steering pump and the air conditioning compressor. Meanwhile, the same component in the RAV4 can be readily accessed from the top, requiring less effort. Often, getting to the trouble spot can be just as involved as the actual repair work.
Car owners should know that repair estimates are just that, estimates. Actual costs may be higher as additional problems can arise once the work is underway. Reputable shops will contact you when extra repairs are required or the costs exceed a certain threshold (like 10% above the original estimate). Sometimes, local regulations mandate how a shop needs to handle repairs above the original estimate.
Repair estimates can vary significantly between shops for the same repair. The contrast comes from:
A crucial element of the repair process involves replacement parts. Depending on the repair, your vehicle, and the service center, these components fall into three categories:
While OEM parts are often the preferred choice for many car owners, the cost can be prohibitive. A quality-restored component backed up by a warranty can be a wallet-friendly alternative. Aftermarket parts used in less critical areas can also be cost-effective. Based on your repair, most independent repair shops will explore your options as part of the estimate process.
Parts availability is a valid concern in a post-pandemic automotive world. While supply chain issues have largely subsided, it’s not unheard of to encounter delays with some components. In these situations, repair shops and their customers have to explore alternatives, which may require going with an OEM part over something remanufactured or vice versa. Good shops will have access to multiple parts sources, ensuring timely repairs.
Once replacement parts have been lined up, repair work can begin. These efforts may involve:
Conscientious auto technicians follow precise repair procedures and may have to use brand-specific tools. Many shops employ technicians with ASE (Automotive Service Excellence) certifications or brand-specific training to ensure vehicle repairs meet industry standards. A complex repair often requires the services of expert technicians who have advanced experience, including factory training. It’s not unusual for general repair shops to contract with specialized service operations for certain work, like on transmissions.
Following the successful completion of repairs, a responsible shop will conduct a quality check before returning the car. These final inspection steps might include:
During pickup, the shop will present a final invoice. The amount may differ somewhat from the original invoice, but should fall within the agreed price or maximum estimate range. If you’re lucky, you might even pay less than the estimate, due to work being performed more quickly or parts costing less than originally anticipated. The final bill will cover labor, parts, supplies, fees, any additional authorized work, and sales tax.
With car parts being sold online, it can be tempting to compare what the shop charges you versus e-commerce retailers. Don’t be surprised if the repair bill comes with a 25% to 50% markup on parts. You’re dealing with a local business that has to pay for mechanics’ salaries and the cost of maintaining a garage, expenses that online sellers don’t have to worry about. In addition, a trusted repair shop stands behind its work and assumes responsibility for proper fitment and function.
Uncertainty about car repair costs can be stressful for an owner, especially if the vehicle isn’t covered by a factory warranty. In this situation, an extended car warranty (also called an auto protection plan or vehicle service contract) can provide peace of mind and protection against costly repairs and breakdowns.
Consider the advantages of an Endurance Warranty plan:
Learn more about Endurance Warranty by requesting a FREE email quote or visiting the Endurance online store for instant plan and pricing information. Endurance plan advisors are also available by phone at (800) 253-8203.
Explore the Endurance blog for insight articles about car care, DIY maintenance, ownership topics, car reviews, and more.
We've received your vehicle information and will contact you shortly with your quote.
— OR —
Start shopping for a coverage plan now.
We're here to make sure you get the most comprehensive EV protection. That's why we've partnered with Xcelerate Auto to offer you transparent and dependable Tesla coverage.
Want us to contact you about XCare coverage for your Tesla?
Your protection is our top priority. Your quote is in progress and you will
receive a confirmation
email shortly.
Speak with a vehicle protection plan specialist and get $300 off any new contract instantly.
Call for $300 off any new plan!
By clicking the button, you consent to Endurance using automated technology to call, email, and text you using the contact info above, including your wireless number, if provided, regarding auto protection or, in California, mechanical breakdown insurance. You also agree to the Endurance Privacy Policy and Terms and Conditions. Consent is not a condition of purchase, and you can withdraw consent at any time. Message and data rates may apply.
Speak with a vehicle protection plan specialist and get $300 off any new contract instantly.
Call 866-678-4172
or scan the code below
Simply fill out the information below and we will follow up fast with your free no-obligation quote.
By clicking the button, you consent to Endurance using automated technology to call, email, and text you using the contact info above, including your wireless number, if provided, regarding auto protection or, in California, mechanical breakdown insurance. You also agree to the Endurance Privacy Policy and Terms and Conditions. Consent is not a condition of purchase, and you can withdraw consent at any time. Message and data rates may apply.
To speak to a vehicle protection plan specialist and save $300
Scan the code below
Since the age of 16, Keith has been immersed in the automotive industry, beginning his career by helping his dad fix vehicles at a young age. Keith now owns his own family-run, ASE Certified repair shop, A+ Autocare. At his shop, he focuses on building trusting relationships with his community through exceptional customer service. Read more about Keith.